CASTELLÓ. El sector de la cerámica emplea en España a 16.000 personas de forma directa y genera cerca de 26.000 empleos indirectos e inducidos. Su industria es una de las más prósperas de nuestra economía, siendo España el primer exportador en volumen de la Unión Europea y el segundo a nivel mundial. No obstante, el sector de los productos cerámicos se enfrenta a uno de los desafíos más importantes de su historia: la digitalización de sus diferentes etapas de producción.
Un reto este, si cabe, que presenta mayor dificultad en un entorno industrial lleno de fábricas con enormes capacidades de producción, algunas de ellas entre las más importantes del mundo en este tipo de productos, respecto a otras industrias.
Desde Sothis, compañía líder especializada en el desarrollo e implantación de soluciones integrales de digitalización en varios sectores y con amplia experiencia en el sector cerámico, consideran necesario el avance del sector hacia una industria inteligente que conecte nuevas necesidades y procesos productivos.
“Uno de los grandes retos que presenta la industria cerámica es el hecho de que las máquinas y equipos responsables de cada fase de fabricación no estén conectados entre sí. La falta de automatización de los procesos de fabricación, del flujo de datos e información limita la eficiencia general de los equipos y de la producción”, explica Luis Beltrán, director comercial de la unidad de negocio Ingeniería y consultoría digital de Sothis.
Industrial Internet of Things (IIoT): sensorización y datos para optimizar la producción
En un mercado global en continua evolución, las industrias necesitan monitorizar, gestionar y controlar sus activos para dotarlos de inteligencia y hacer un uso útil de la información en tiempo real. Para ello, el primer paso que deben dar las compañías del sector cerámico es adecuar su cadena de suministro a la Industria 4.0.
“En las fábricas del futuro, la excelencia operacional y la eficiencia en el uso de los recursos pasan por una integración perfecta de la cadena de suministro, de principio a fin. Todas las capas y fases de la producción deben estar más cerca que nunca y, aquí, el sector debe servirse de las oportunidades que ofrecen las últimas tecnologías como el Internet de las cosas (IoT, o IloT en su versión industrial)”, sentencia Luis Beltrán.
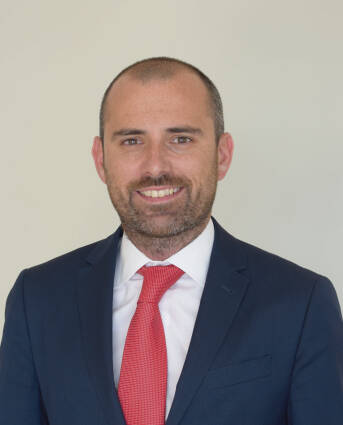
La hiperconectividad es la clave para impulsar la eficiencia y la innovación en la nueva era industrial. El IoT ofrece la comunicación perfecta entre personas, máquinas y procesos, permitiendo monitorizar todo el proceso productivo para obtener datos operacionales relevantes y en tiempo real de todo el sistema. Esto se traduce en ayuda a la hora de optimizar la planificación, reducir costes, mejorar la trazabilidad, contar con información única para una toma de decisiones coordinada, ganar visibilidad de indicadores clave, realizar un mantenimiento predictivo o prever y evitar fallos de producción. En definitiva, optimizar cualquier proceso y facilitar la innovación de producto, proceso e incluso modelo de negocio.
Al mismo tiempo, el IoT ofrece la posibilidad de hacer frente a otro de los grandes retos actuales y futuros de la industria: la sostenibilidad. Las fábricas de productos cerámicos utilizan en sus procesos hornos a altas temperaturas que consumen grandes cantidades de energía. Aquí, la tecnología IoT y el software de gestión permiten realizar mediciones de consumo en las instalaciones, permitiendo controlar y mejorar la eficiencia energética del espacio y contribuir a un modelo productivo más sostenible y eficiente energéticamente.
Sistemas de fabricación basados en gemelos digitales
El Gemelo digital es el otro gran baluarte de la Industria 4.0. Un gemelo digital permite contar con un modelo virtual de una planta que ayuda a predecir cambios y optimizar inversiones. Desde Sothis, esto se logra con Tecnomatix, la solución de Gemelo Digital de Siemens que permite la simulación tanto de la planta (Tecnomatix Plant Simulation). así como de los diferentes procesos que intervienen en la cadena productiva (Tecnomatix Process Simulate).
Un gemelo digital, o digital twin –como se le conoce en el mundo anglosajón, donde más implantación tiene– es mucho más que la representación digital del mundo físico. Es donde ambos convergen, sirviendo como el puente entre objetos, procesos y sistemas y un mundo de datos que desbloquea posibilidades hasta ahora inéditas.
“Si implementamos un gemelo digital del proceso productivo, podemos ser más ágiles. Antes, los formatos de producción eran mucho más estándar y ahora, la demanda del mercado exige que haya una mayor variedad para un mismo producto. Si desde el diseño de producto diseñamos el azulejo, por ejemplo, con nuevas dimensiones, podemos utilizar el gemelo para comprobar si las máquinas soportan el nuevo formato, o cuál será mi capacidad productiva con las instalaciones actuales. Como ves, una de las mejoras que lograremos con este tipo de soluciones, es la validación de nuevas inversiones y la implantación de nuevas líneas de producción”, destaca Luis Beltrán.
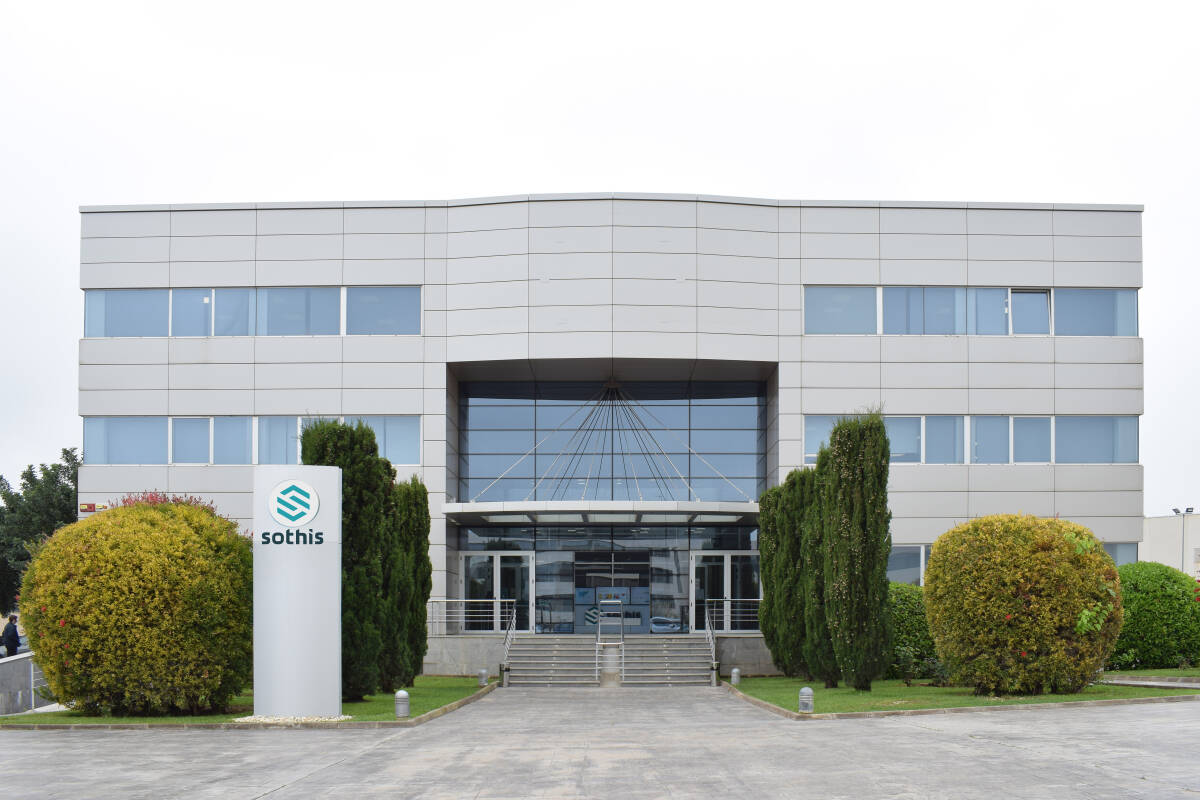
En definitiva, los gemelos digitales abren un abanico de posibilidades cada vez más amplio a medida que su tecnología madura. Los casos que el portavoz de Sothis señala son solo algunos ejemplos en ámbitos de actuación de cómo la convergencia tecnológica entre el mundo físico y el digital está cambiando este sector.
Realmente, son un terreno altamente disruptivo que, sin duda, está transformando la manera en la que abordamos nuestra manera de trabajar con datos, haciéndolos más complejos y ricos para, en última instancia, optimizar la toma de decisiones en tantos ámbitos como queramos imaginar y ayudarnos a resolver los retos más desafiantes del presente y el futuro.
Gres Aragón: MOM para la digitalización en planta
Un gran conocimiento del sector, de las capacidades tecnológicas de sus procesos y la figura de acompañamiento que ejercen ha permitido a la consultora tecnológica Sothis consolidarse en el sector cerámico con la adjudicación de importantes proyectos de digitalización de procesos de fabricación. Por el camino, Sothis ha trabajado para clientes como Gres Aragón, con más de 75 años de experiencia en el sector cerámico, un catálogo con gran diversidad de soluciones para espacios exteriores e interiores, y aplicaciones en pavimentos, escaleras, piel de edificios y piscinas, aplicando la tecnología productiva más vanguardista.
Gres Aragón cuenta con un gran componente tecnológico, disponiendo de maquinaria avanzada y un departamento de I+D+i enfocado en la creación y diseño de nuevos productos. En su apuesta por la modernización e innovación, Gres Aragón ha implantado un proyecto integral de digitalización de su proceso productivo desde la parte de planificación y secuenciación avanzada de la producción (módulo APS) hasta el seguimiento y control de la producción en planta en tiempo real (módulo MES) dentro de la suite Opcenter de Siemens, la solución integral más avanzada en la gestión de operaciones de fabricación (o MOM, por sus siglas en inglés) del mercado, utilizada para la planificación y programación avanzadas de las plantas de producción.
El objetivo de este proyecto de digitalización es mejorar la sincronización de los procesos de producción de Gres Aragón, obteniendo una mayor visibilidad y optimizando el aprovechamiento de recursos, la puntualidad de las entregas, reduciendo los niveles de inventario, pérdidas y tiempos de planificación, así como realizar mantenimientos preventivos más precisos y dotarse de mayor capacidad de reacción y replanificación ante imprevistos como roturas de máquinas.
“Cada vez más empresas, como Gres Aragón, se han dado cuenta de que la digitalización ha dejado de ser un claim y que el sector, que cuenta con procesos de fabricación avanzados y exigentes, puede beneficiarse de una apuesta decidida por la tecnología de medición y optimización en planta”, finaliza Luis Beltrán.
Descubra más sobre Sothis y sus soluciones en https://www.sothis.tech/